The Industrial Internet of Things (IIoT) is revolutionising various aspects of industrial operations, bringing unprecedented efficiencies and capabilities. Among the areas experiencing significant transformation are repair, maintenance, and warranty management.
By leveraging IIoT and connected technologies, businesses can streamline these processes, reduce costs, enhance customer satisfaction, and improve overall operational efficiency.
This blog explores 5 ways in which IIoT is reshaping repair, maintenance, and warranty management.
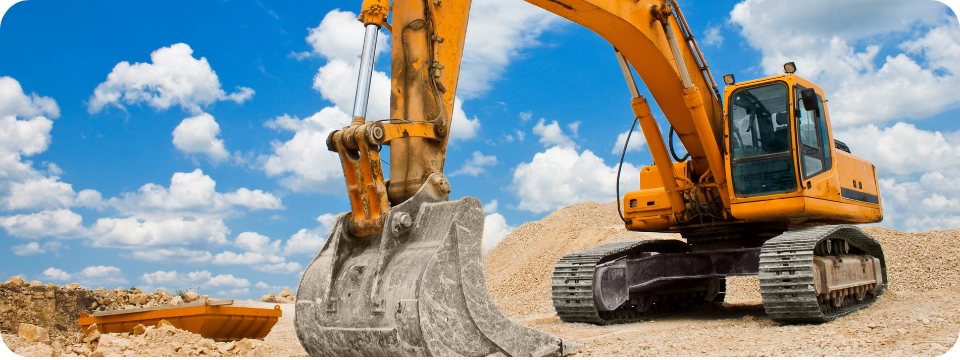
1. Enhancing predictive maintenance
Predictive maintenance is one of the most transformative applications of IIoT in industrial settings. Traditional maintenance methods often rely on scheduled or reactive approaches, which can lead to unexpected downtimes and higher costs. IIoT changes this dynamic by enabling continuous monitoring and data analysis.
Real-time data collection and analysis
IIoT devices equipped with sensors collect real-time data on various parameters such as temperature, pressure, vibration, and humidity. Advanced analytics and machine learning algorithms process this data to predict potential failures before they occur. This predictive approach allows for timely interventions, minimising downtime and extending the lifespan of equipment.
Benefits of predictive maintenance
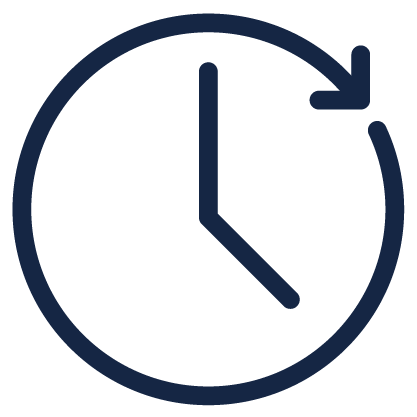
1. Reduced downtime
By identifying issues before they lead to breakdowns, businesses can plan maintenance activities during non-peak hours, thus reducing operational disruptions.
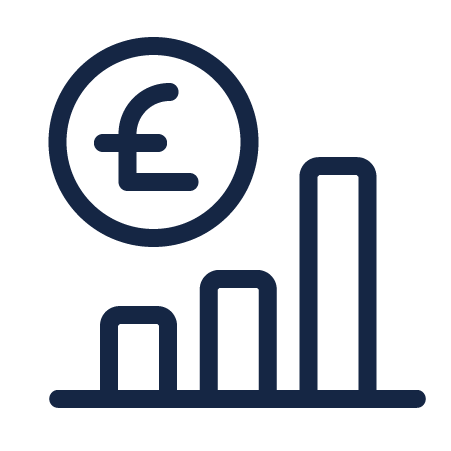
2. Cost savings
Preventive actions are generally less expensive than emergency repairs. Predictive maintenance helps in optimising resource allocation, reducing unnecessary parts replacement, and labour costs.
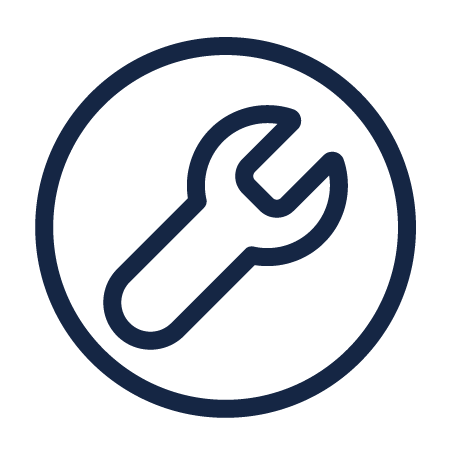
3. Extended equipment life
Consistent monitoring and timely maintenance keep equipment in optimal condition, thereby extending its useful life.
2. Streamlining repair processes
IIoT also significantly improves the efficiency and effectiveness of repair processes. Through connected technology, businesses can enhance their repair operations in several ways.
Remote diagnostics and troubleshooting
Connected devices enable remote diagnostics, allowing technicians to analyse and troubleshoot issues without being physically present. This capability reduces the need for on-site visits and accelerates the repair process.
Real-time support and guidance
IIoT systems can provide real-time support and guidance to on-site technicians. For instance, augmented reality (AR) applications can overlay digital instructions onto physical equipment, guiding technicians through complex repair procedures.
Automated workflows
IIoT can automate various repair-related workflows, such as fault detection, reporting, and parts ordering. Automated alerts notify technicians of issues, while integrated systems can automatically order replacement parts based on diagnostic data. This automation reduces administrative overhead and speeds up the repair process.
3. Optimising warranty management
Warranty management is another area where IIoT and connected technology bring significant improvements. Traditional warranty processes often involve manual tracking and paperwork, which can be time-consuming and error-prone. IIoT streamlines and enhances warranty management in several ways.
Automated warranty tracking
IIoT devices can automatically log operational data and track equipment usage. This data provides a detailed record of equipment performance, which can be used to verify warranty claims. Automated tracking ensures accurate and up-to-date warranty information, reducing the likelihood of disputes.
Enhanced warranty analytics
By analysing data collected from connected devices, businesses can gain insights into common failure patterns and warranty claim trends. This information can help manufacturers improve product design and quality, reducing the number of warranty claims.
Proactive warranty service
IIoT enables proactive warranty service by identifying potential issues before they lead to failures. Manufacturers can offer preemptive repairs or replacements under warranty, enhancing customer satisfaction and reducing overall warranty costs.
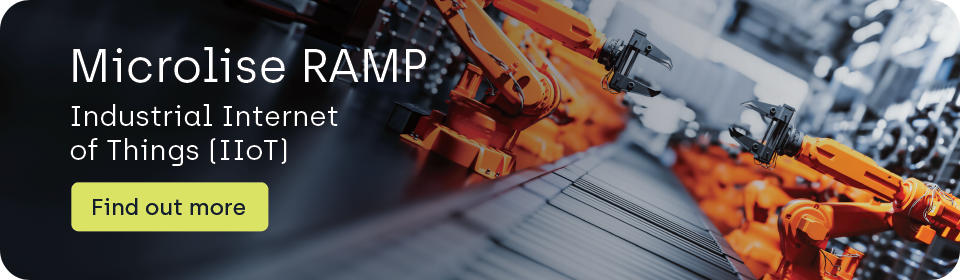
4. Improving customer satisfaction and engagement
IIoT and connected technologies play a crucial role in improving customer satisfaction and engagement. By offering more reliable equipment, faster repairs, and proactive maintenance, businesses can significantly enhance the customer experience.
Personalised service
Data collected from IIoT devices provides a detailed understanding of each customer’s equipment usage and performance. This information allows businesses to offer personalised service recommendations and support, tailored to the specific needs of each customer.
Proactive communication
IIoT enables proactive communication with customers. For example, if a potential issue is detected, the service team can notify the customer and schedule maintenance before a failure occurs. This proactive approach builds trust and demonstrates a commitment to customer care.
Faster response times
Connected technology ensures that service teams are immediately alerted to any issues, enabling faster response times. Quick resolution of problems leads to higher customer satisfaction and loyalty.
5. Driving operational efficiency
The integration of IIoT and connected technology drives overall operational efficiency in repair, maintenance, and warranty management.
Data-driven decision making
IIoT provides a wealth of data that can be used to optimise maintenance schedules, repair processes, and warranty policies. Data-driven decision-making ensures that resources are used efficiently and effectively.
Resource optimisation
By predicting maintenance needs and automating repair workflows, businesses can optimise the use of their resources. This optimisation includes better scheduling of technicians, efficient parts inventory management, and reduced downtime.
Continuous improvement
The insights gained from IIoT data enable continuous improvement in operations. Businesses can identify areas for improvement, implement changes, and monitor the impact of these changes over time. This continuous improvement cycle leads to increased efficiency and better service outcomes.
Conclusion
The Industrial Internet of Things (IIoT) and connected technologies are transforming repair, maintenance, and warranty management by enabling predictive maintenance, streamlining repair processes, optimising warranty management, and enhancing customer satisfaction. By leveraging real-time data, automation, and advanced analytics, businesses can achieve significant cost savings, improve operational efficiency, and provide superior service to their customers. As IIoT continues to evolve, its impact on repair, maintenance, and warranty management will only grow, driving further innovations and improvements in the industrial sector.