Working With Industry Leaders
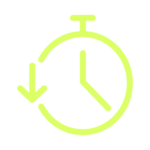
Reduce downtime
Predict and prevent equipment failures, keeping your operations running smoothly.
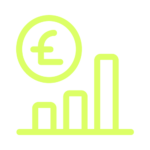
Cost savings
Lower maintenance costs by addressing issues before they become major problems, extending the lifespan of your equipment.
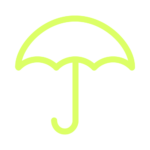
Improve safety
Identify potential hazards early, ensuring a safer work environment for your employees.
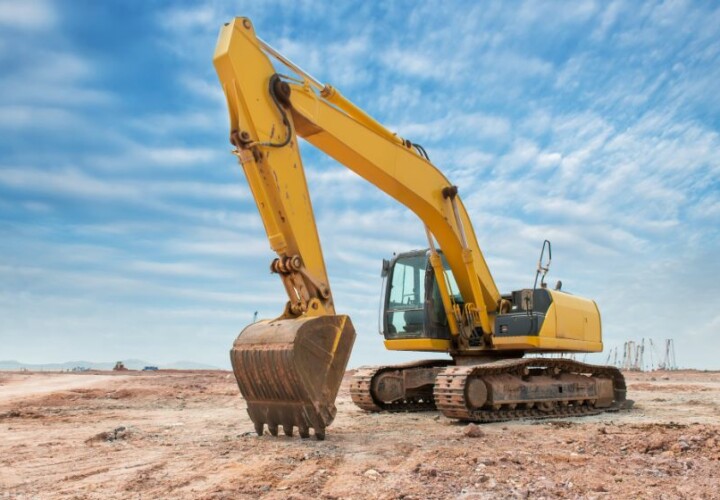
24/7 asset monitoring
Our predictive maintenance tools utilise analytics and machine-learning algorithms to continuously collect and analyse data from your machinery with minimal human intervention, providing real-time insights into the health and performance of your equipment.
Our software identifies patterns and anomalies that might be missed by traditional maintenance methods, allowing you to make data-driven decisions, predict potential failures and act proactively.
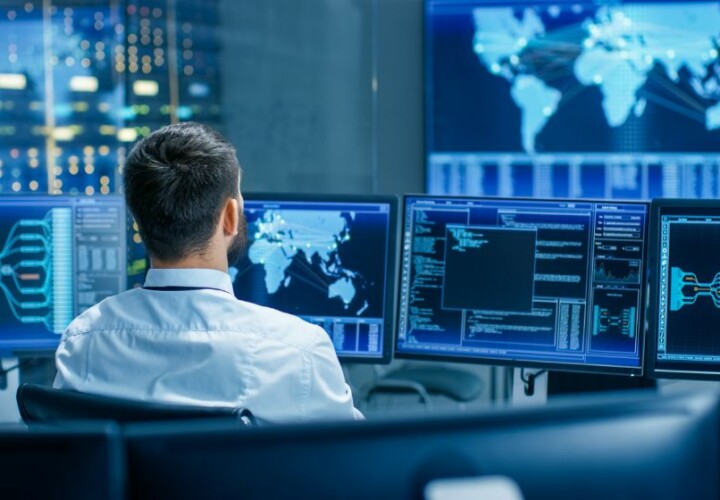
Configurable dashboards
Analyse and share historical and real-time data through customisable dashboards, allowing for proactive maintenance decisions. Produce dashboards showing:
- Equipment performance
- Maintenance activities
- Data-based maintenance predictions
You can also:
- Define user visibility by assigning keywords and user groups to dashboards
- Set up custom alerts to notify your team about potential issues before they escalate
- Receive notifications via email, SMS, or in-app messages, ensuring you're always in the loop
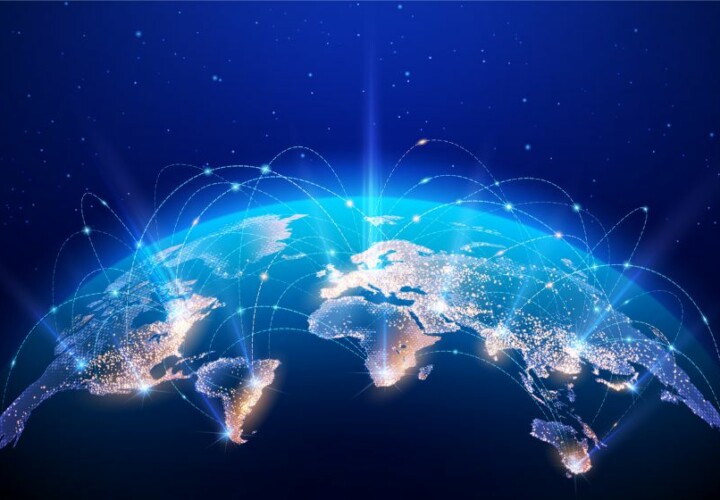
Scalable and flexible
Whether you have a single facility or multiple locations, our predictive maintenance software scales to meet your needs. Manage all your equipment from a centralised platform.
Frequently asked questions
Predictive maintenance is a proactive approach that uses data analytics and machine learning to predict equipment failures before they occur. By analysing data from sensors and other monitoring tools, it identifies patterns and anomalies indicating potential issues. This enables timely maintenance actions, preventing unexpected breakdowns, reducing downtime, and extending equipment lifespan. Predictive maintenance is critical for enhancing operational efficiency, safety, and cost-effectiveness in industries such as manufacturing, energy, transportation, and healthcare, where equipment reliability is vital.
Predictive maintenance software uses data analytics and machine learning to predict equipment failures before they occur. By analysing data from sensors and other monitoring tools, it identifies patterns and anomalies that indicate potential issues. This proactive approach allows maintenance to be performed at optimal times, reducing downtime, extending equipment lifespan, and lowering maintenance costs. Predictive maintenance software is essential for industries like manufacturing, energy, and transportation, where equipment reliability and operational efficiency are critical.
Predictive maintenance software benefits industries where equipment reliability and operational efficiency are crucial. In manufacturing, it helps prevent costly production halts by predicting machine failures. The energy sector uses it to maintain infrastructure and avoid power outages. Transportation relies on it for fleet management, ensuring vehicles operate safely and efficiently. In healthcare, predictive maintenance ensures medical equipment remains functional, reducing downtime and improving patient care. The oil and gas industry uses it to maintain critical infrastructure and avoid environmental hazards, enhancing overall safety and efficiency.
Predictive maintenance is important because it enables organisations to anticipate equipment failures before they happen, reducing unplanned downtime and extending the lifespan of machinery. By using data analytics and machine learning, predictive maintenance helps identify potential issues early, allowing for timely interventions that prevent costly repairs and operational disruptions. This approach improves overall efficiency, enhances safety, and reduces maintenance costs, making it critical for industries like manufacturing, energy, and transportation where equipment reliability and operational continuity are essential.