In today's fast-paced industrial landscape, manufacturers are continuously seeking ways to enhance efficiency, reduce costs, and improve product quality.
The Industrial Internet of Things (IIoT) has emerged as a transformative technology that connects the various facets of the manufacturing process, leading to smarter and more agile operations.
This blog explores how IIoT technology is revolutionising the manufacturing industry by connecting processes, equipment, and people like never before.
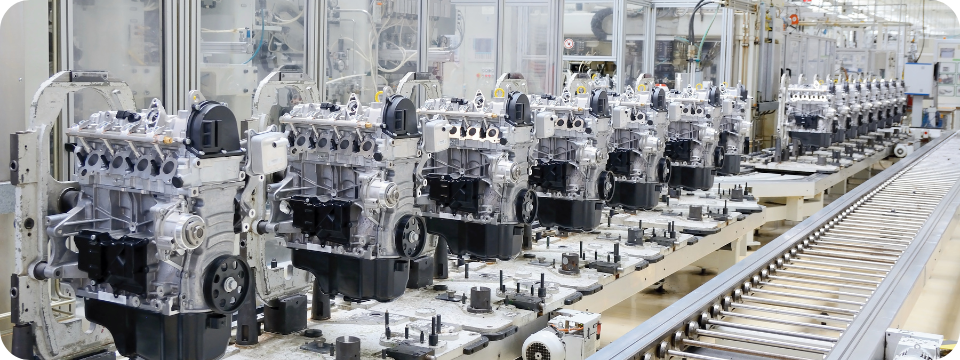
What is IIoT?
The Industrial Internet of Things (IIoT) refers to the integration of internet-connected devices in the industrial sector. These devices range from sensors and actuators to advanced robotics and machine learning systems. By collecting and analysing data in real-time, IIoT enables manufacturers to make informed decisions, automate processes, and optimise operations.
Find out more: What is Industrial Internet of Things?
Enhancing operational efficiency
Real-time monitoring and control
One of the primary benefits of IIoT in manufacturing is real-time monitoring and control. Sensors embedded in machinery and equipment continuously collect data on various parameters such as temperature, pressure, and vibration. This data is then transmitted to a central system where it can be analysed in real-time.
With this capability, manufacturers can detect anomalies and address issues before they escalate into major problems. For example, if a sensor detects an unusual vibration in a motor, the system can trigger an alert, allowing maintenance teams to intervene promptly. This proactive approach reduces downtime and ensures that equipment operates at optimal efficiency.
Predictive maintenance
Traditional maintenance strategies often rely on scheduled inspections and repairs, which can be inefficient and costly. IIoT enables predictive maintenance by using data analytics and machine learning to predict when equipment is likely to fail. By analysing historical data and identifying patterns, IIoT systems can forecast maintenance needs with high accuracy.
Predictive maintenance software minimises unplanned downtime, extends the lifespan of equipment, and reduces maintenance costs. It also allows manufacturers to allocate resources more effectively, ensuring that maintenance efforts are focused on the most critical assets.
Optimising production processes
Improved quality control
Quality control is a critical aspect of manufacturing, and IIoT plays a significant role in enhancing it. By collecting data at every stage of the production process, IIoT systems can identify deviations from quality standards in real-time. This immediate feedback enables manufacturers to take corrective actions swiftly, reducing the likelihood of defective products reaching the market.
Additionally, IIoT can facilitate the implementation of advanced quality control techniques such as Statistical Process Control (SPC). By continuously monitoring production variables, SPC can detect trends and variations that indicate potential quality issues, allowing manufacturers to address them proactively.
Supply chain integration
IIoT technology extends beyond the factory floor, connecting the entire supply chain. By integrating data from suppliers, manufacturers, and distributors, IIoT provides a comprehensive view of the production process from raw material procurement to final product delivery.
This integration enables better coordination and collaboration among supply chain partners. For instance, if a supplier experiences a delay, the manufacturer can adjust production schedules accordingly to minimise disruptions. Similarly, real-time inventory tracking allows manufacturers to maintain optimal stock levels, reducing the risk of overstocking or stockouts.
Find out more: How IIoT and connected technology can transform your distribution network
Enabling smart manufacturing
Automation and robotics
Automation is a cornerstone of modern manufacturing, and IIoT takes it to the next level. By integrating IIoT with advanced robotics and artificial intelligence (AI), manufacturers can create smart factories where machines communicate and collaborate seamlessly.
Robots equipped with sensors and connected to the IIoT network can perform complex tasks with precision and adaptability. For example, in an assembly line, robots can adjust their actions based on real-time feedback from sensors, ensuring consistent quality and efficiency. This level of automation not only increases productivity but also allows human workers to focus on higher-value tasks.
Digital twin technology
Digital twin technology, a key component of IIoT, involves creating a virtual replica of a physical asset or process. This digital twin continuously receives data from its physical counterpart, enabling manufacturers to simulate, analyse, and optimise operations in a virtual environment.
By using digital twins, manufacturers can test different scenarios, identify potential improvements, and make data-driven decisions without disrupting actual production. For instance, they can simulate the impact of a new production line configuration or evaluate the performance of a new material before implementation. This capability accelerates innovation and reduces the risk associated with changes.
Improving safety and sustainability
Enhanced worker safety
IIoT technology contributes significantly to improving worker safety in manufacturing environments. Wearable devices equipped with sensors can monitor workers’ health and safety conditions in real-time. For example, wearable devices can track heart rate, body temperature, and exposure to hazardous substances, alerting workers and supervisors to potential risks.
Furthermore, IIoT can enhance safety protocols by automating hazardous tasks and ensuring that machinery operates within safe parameters. In case of an emergency, IIoT systems can trigger immediate shutdowns and alerts, minimising the risk of accidents and injuries.
Environmental sustainability
Sustainability is a growing concern for manufacturers, and IIoT can help address this challenge. By optimising energy consumption, reducing waste, and improving resource utilisation, IIoT contributes to more sustainable manufacturing practices.
For example, IIoT systems can monitor energy usage in real-time, identifying opportunities for energy savings and efficiency improvements. Additionally, IIoT can facilitate the implementation of circular economy practices by tracking the lifecycle of materials and enabling recycling and reuse initiatives.
Conclusion
The Industrial Internet of Things (IIoT) is revolutionising the manufacturing process by connecting machines, processes, and people in unprecedented ways. From real-time monitoring and predictive maintenance to improved quality control and supply chain integration, IIoT offers numerous benefits that enhance operational efficiency, optimise production processes, and enable smart manufacturing.
As manufacturers continue to embrace IIoT technology, they can expect to achieve higher levels of productivity, safety, and sustainability. The future of manufacturing is undoubtedly connected, and IIoT is at the forefront of this transformative journey.